Master tailors are not confined to the town houses of Savile Row or the ateliers of Italy; with the boom in Asian prosperity has come a boom in Asian style. Erica Wong speaks to a Singapore-based tailoring maestro about his unique style
Shi Fu, or master, as Thomas Wong is commonly referred to, asks if I’d like a cup of tea as I take a seat next to him at a quaint coffee shop along Orchard Road. His tone is calm and certain, almost Mr. Miyagi-like. Chairman of the Master Tailor Association Singapore for the last two terms, lecturer at the LASALLE College of the Arts, and owner of one of the oldest tailor shops on the island, Wong has been making suits for the regions’ elite for well over four decades. The industry has changed much but the fundamentals remain the same, as Wong explains…
EW You’ve seen the industry through thick and thin…
TW I started in this line of work when I was 16. I was an apprentice and at that time shops in Singapore were in shophouses. Each shop housed their entire ‘production line’ from start to finish. Tailors trained their teams to do everything from scratch in their own character using their unique methods. As a result every shop has their own style, their own ideas about how to make a suit. The team would discuss the orders or any problems that arose, work out solutions together, which would reflect the philosophies of the brand. If a customer finds that ‘chemistry’ with Tailor A or B or C, they would consistently return to them. There was no competition between A, B or C because they each had their unique cut, style, quality and fit which was very different from one another. Without intentionally doing so, each tailor was a ‘brand’.
Today, the shophouse ‘all under one roof’ concept is gone. Tailors outsource the different parts of the job to independent workers who at times sub-outsource out, since there are only a handful of craftsmen who know how to do each job. Most of these independent workers accept jobs from a number of tailors so you can imagine how the original set up of the tailor ‘brand’ has been lost, the traditional collaborative production lines severed and the uniqueness of each brand has been diluted. The tailor’s role has become that of a coordinator who charges a middle-man fee. In my mind, that’s not a tailor. To be a bespoke tailor, you need to make a particular garment per a customer’s particular request. Instead, tailors are now middle-men who take the request and pass the garment around to various parties who make it in whichever way they know best. This isn’t a very responsible way of offering the bespoke tailoring service.
EW What is at the core of your design ethos?
TW I’ve always been interested in illustration and so naturally in [Chinese] calligraphy. I believe that when people are interested in the visual arts they have sensitivities towards the minute details. Whether that dark green is the right tone or the stripe is slightly too wide, the demand for perfection is innate. When it comes to designing or making patterns or cutting fabric, I apply that same temperament and attitude. Throughout every step of the process I keep thinking about how the suit will fit on the client. Should this cut, length or even shadow appear on his frame? Will the suit look forced or natural on him? Wearing clothes need to be a comfortable affair. If the suit isn’t comfortable or doesn’t make its owner feel better about himself, he winds up as a hangar for the clothes. Then he might as well not wear it at all. The person cannot be a mannequin for the suit, the suit must highlight the man’s strongest features. Of course as a bespoke tailor I need to adhere to the client’s requests so I also need to fit my design into the parameters of his request. This is the challenge.
For example if a larger man wants a double-breasted suit even though most tailors might think it a bad idea, I try to figure out how to not only defy the theories against it but to make him look slim in the cutting of his choice. How should I do the cutting? What kind of fabric should I recommend? What fabric patterns will be the better option? The quality of the fabric also makes a difference. So, in-depth knowledge about all these factors is imperative for a bespoke tailor. Even before you take the job, you need to offer your professional opinions. If you don’t have the fundamental basis and you deliver exactly what the client asks for, then you’ve escaped your responsibilities.
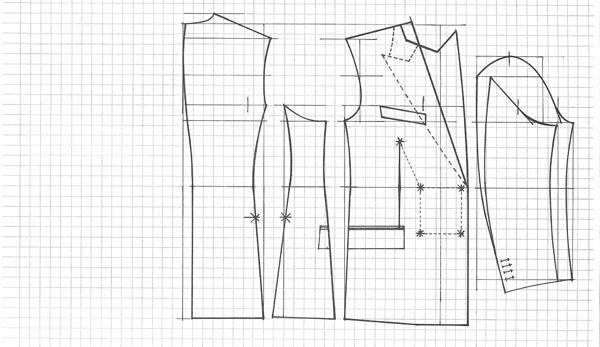
Every aspect — the cut, darts, seams, fabric and accents — plays an important role in the final product
EW With 40 years of accumulated knowledge, what are the main lessons that you relay to your students?
TW Firstly, never take short cuts. Not in any step of the process.
Equally important is to work with integrity. Other players in the field have asked why suppliers provide me with top quality work and lesser quality to them. The answer is very simple. An analogy I often give is a woman who sees her friend’s perfect glowing skin after leaving the spa and requests to achieve the same results. But if she’s not willing to pay for the same top quality skin care products or use the same top aesthetician, how can she expect the same results? It’s just not possible. The same applies for my craftsmen. Everyone may share the same pool of talent but if I pay top prices for top quality and others aren’t willing to do the same, who do you think will be given priority? It’s a simple formula. I always tell my students that we can’t deliver anything sub-par because the dollar notes customers give us are not partial dollars. The $1,000 they give us is $1,000, no less. So if you charge $1,000 you can’t provide a $100 product.
EW There seems to be less and less people who fit into your traditional sense of a tailor. Where do you see the industry heading?
TW Last year, the Asia Tailor’s Congress was held in Singapore and it was Loro Piana who noted that Singapore’s tailors aren’t charging enough. Times have changed and yet we continue to charge low prices so our pricing strategy benefits the end customer, and we don’t pay our workers enough. That’s why less and less people are entering the field and those who are skilled have turned to other lines of work such as driving taxis, which is more lucrative.
What’s more, there’s an interesting phenomenon at play today. Technically the more affluent the country, the better their know-how ought to be and the more demanding the customer, and yet they try to take shortcuts. On the flip side, the poorer the country, the more traditionally trained craftsmen they have, and yet the market generally can’t afford the good fabrics and infrastructure to produce the suits. Over the long run, I hope to see a revival of the traditional crafts and skills, applied in modern contexts. That’s why I teach, in hope that my students will pick up some of the things I learnt many years ago, and apply them in their future careers.
Awesome post! I really liked reading about Shi Fu’s life and how the industry has changed! Very interesting point of view.